摘要
在本设计说明书中,我通过对零件的图形分析,零件的结构工艺性,技术要求进行仔细分析了,所设计的零件结构应便于成型,并且成本低,效率高,它的涉及面广,因此这一环节是技术的关键,以便在拟定工艺规程时采用适当的措施。材料分析,选好了加工毛坯,了解常用的毛坯种类:锻件.型材.焊接件.冷压件等,还有毛坯是根据零件要求的形状,工艺尺寸等方面而制成的进一步加工使用的生产对象。在制订零件的工艺规程时,正确的选择工件的基准有着很重要的意义,应划分阶段一般分粗加工.半精加工和精加工三个阶段。选择的机床型号是CA6140普通车床,CJ6032A教学型数控车床。另外还对加工的工序.工艺进行分析,从而手工将加工零件的全部工艺过程、工艺参数、位移数据等以规定的代码、程序格式写出,编制出了适合所选车床的程序。
关键词: 零件的分析,毛坯,工艺,工序尺寸,加工路线,编程
零件的形状分析
轴系组合件较为复杂,从外形上看件一左端是不完整的球端面.球端的边面质量Ra1.6.外阶梯形圆柱表面质量Ra1.6,车40度的槽及椭圆左端的槽,内孔螺纹等的加工难度较大内边面质量Ra1.6,右端外部椭圆留双边1 mm。件二是椭圆,阶梯形圆柱质量Ra1.6, 外螺纹加工精度都很高。
大体加工过程:加工件加工件二:首先在车床上用外圆车刀粗加工,倒角,车外螺纹,用外圆车刀车椭圆,然后用手工切断.加工加工件一:先在车床用外圆粗车加工球面,车40度槽,倒角,内孔镗刀加工内孔,切内孔φ31的槽,然后车M30X1.5的内螺纹,最后外圆车刀加工椭圆.
1.1.2 零件的技术要求分析
零件图纸上标注的技术要求:
1.锐边倒角C0.3
2.未注倒角C1.
3.圆弧过渡光滑
4.未注尺寸公差按GB/T1804-m加工和效验
5.调质硬度HRC30-35
1.1.3 零件的加工表面的分析
从零件图可以看出轴系零件的主要加工表面是:
1. φ31的槽:它的表面粗糙度是Ra1.6,而且其轴心线是设计基准。
2.M30×1.5-6H的螺纹:此螺纹是一个标准螺纹,虽然没有特殊要求,但它在配合时起传递扭矩的作用,故其配合精度要求高。
3.椭圆:表面粗糙度Ra3.2, 轴心线是设计基准。
4.球面:尺寸以确定,表面粗糙度Ra1.6,圆心是设计基准.
通过以上的分析可知,零件的结构较为简单,易于加工,具有一定的可行性。
1.2 零件的材料分析
零件材料的选用是非常重要的,选材不当制成的零件不能满足使用要求,过早损伤和破坏产生不良影响或经济效益差等。机械零件选材的一般原则是:首先满足使用性能的要求,同时兼顾工艺性、经济性和环保性。对于轴类零件的选材应具有以下几点要求:
1.优良的综合力学性能,即要求有高的强度和韧性,以防止由于过载和冲击而引起的变形和断裂。
2.高的疲劳极限,防止疲劳断裂。
3.良好的耐磨性。
4.在特殊条件工作时,还应有特殊要求。
本零件的材料是45号钢,它属于低淬透性合金调质钢,其力学性能是: MPa, MPa, , , J。其化学成分是:碳含量0.37%~0.45%,铬含量0.8%~1.1%,锰含量0.17%~0.37%,硫含量0.5%~0.8% ,其中碳含量过高、过低均不能满足经调质后获得良好综合力学性能的要求,主加元素为铬,在配以硫、锰等合金元素,其作用是提高淬透性,强化铁素体和细化晶粒,因此,此钢的热处理变形小,废品率低,因而降低了工艺成本。其热处理特点是:当原始组织为珠光体时,预先热处理可采用正火或退火处理;该类钢最终热处理均采用淬火后在500-650℃的高温回火工艺,即调质处理工艺,调质处理可使材料具有良好的综合力学性能。
材料长度的选择:件一取φ50*100,件二取φ50*80的棒料
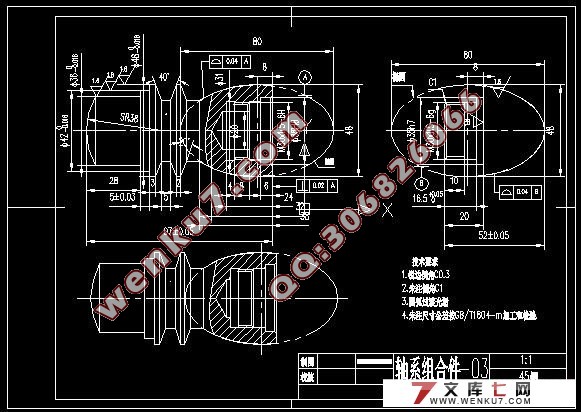
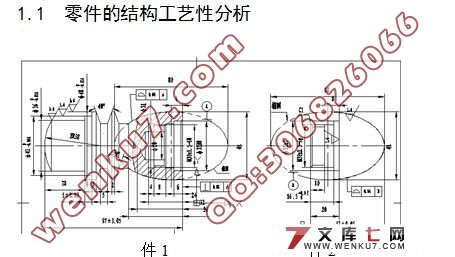
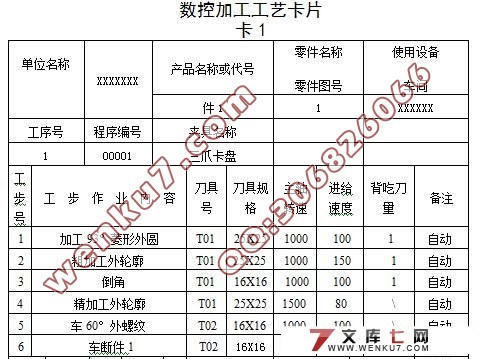
目录 12000字
第一章 零件的分析 ………………………………………………………2
1.1 零件的结构工艺性分析…………………………………………………2
1.1.1 零件的形状分析 ………………………………………………2
1.1.2 零件的形位公差分析 …………………………………………2
1.1.3零件的加工表面分析 ……………………………………………2
1.2 零件的材料分析 ………………………………………………………3
第二章 毛坯的设计 ………………………………………………………4
2.1 确定零件的生产类型和生产纲领 ……………………………………4
2.2.1 毛坯的种类 ……………………………………………………4
2.2.2 毛坯种类的选择 ………………………………………………4
2.2.3毛坯的形状与尺寸的选择 ……………………………………4
第三章 零件工艺规程的设计 ……………………………………………6
3.1 定位基准的的选择 ……………………………………………………6
3.1.1 精基准的选择 ……………………………………………………6
3.1.2 粗基准的选择 ……………………………………………………6
3.2 零件表面加工方法的选择 ……………………………………………7
3.3 加工顺序的安排 ………………………………………………………7
3.3.1 加工阶段的划分 …………………………………………………7
3.3.2 工序的合理组合 …………………………………………………7
3.3.3 加工顺序的安排 ………………………………………………… 8
3.4 工艺的制定 ……………………………………………………………9
3.4.1 工序基准的制定 …………………………………………………9
3.4.2 确定工序尺寸的方法 ……………………………………………9
3.4.3 加工余量的确定 …………………………………………………10
3.4.4 机床的选择 ………………………………………………………11
3.4.5 工艺装备的选择 ………………………………………………11
3.4.6 切削用量的选择 ………………………………………………1
第四章 数控加工程序的编制 …………………………………………………16
4.1 数控加工的特点 ………………………………………………………16
4.2 数控编程方法及特点 ……………………………………………………16
4.2.1 数控编程的分类 ………………………………………………16
4.2.2 编程零点及坐标系的选择 ………………………………………16
4.2.3 对刀点的选择 …………………………………………………16
4.2.4 加工路线的确定 …………………………………………………17
4.3 数控加工程序的内容 ……………………………………………………17
4.3.1车床程序 ……………………………………………………17
结束语 ………………………………………………………………………23
参考文献 ………………………………………………………………………24
|